Filter mesh weaving machine
Mesh size and wire diameter are the most basic structural dimensions of a screen. The ratio of (mesh size/wire diameter) determines the open area of the screen. The relationship between the ratio of (mesh size/wire diameter) f and the open area A of the screen is expressed as follows:
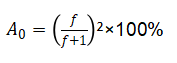
From this equation, it can be seen that square mesh screens with the same (mesh size/wire diameter) ratio have the same open area.
The larger the (mesh size/wire diameter) ratio of a square mesh screen, the greater its open area and the higher the screening efficiency. From the perspective of weaving theory, the (mesh size/wire diameter) ratio of a square mesh screen should not be less than 1, and the minimum limit is 0.7 when the ratio is less than 1. Usually, when weaving a high mesh square mesh with a (mesh size/wire diameter) ratio of 1-1.5, a twill weave is often used. However, when the ratio is greater than 1.35, a plain weave can be used. When the ratio is greater than 1.5, a plain weave is recommended. If a twill weave is used, the warp and weft wires are prone to weave loosely, resulting in a tilted screen. When the ratio is less than 1.35, a twill weave is recommended. If a plain weave is used, a large number of warp wires are likely to break, greatly increasing the difficulty of weaving.
The larger the (mesh size/wire diameter) ratio of a square mesh screen, the smaller the bending angle of the warp and the warp wrap angle. When the thickness of the screen is equal to twice the wire diameter, it means that the warp and weft are equally curved in the screen. However, in reality, the thickness of the woven metal square mesh screen is generally greater than twice the wire diameter. The bending deformation of the warp is greater than that of the weft, which means the bending angle of the warp is greater than that of the weft. In the weaving process, the carding resistance significantly increases, which increases the rate of warp breakage and makes the weaving process more difficult. Typically, the thickness of the screen is 2.2d-2.5d (where d is the wire diameter) regardless of equal or unequal bending deformation of the warp and weft.
Whether it is equal or unequal curvature deformation, as the ratio of hole/thread decreases, the bending angle of the warp thread inside the fabric increases. Therefore, during the weaving process, the warp resistance significantly increases, which leads to a higher rate of warp thread breakage and an obvious increase in the difficulty of the weaving process.